Our Way Through the Years.
Track Record.
Throughout our international trajectory, we have developed industrial robotics and automation solutions in collaboration with strategic partners from various countries. Each project delivered showcases our technical expertise, unwavering commitment to innovation, and dedication to providing customized solutions that drive meaningful impact.
MODENA - ITALY
2007
Robotic cell for welding, deburring, grinding, and protective film incision.
Robotic cell designed for welding and surface finishing of stainless steel parts with thicknesses of 0.8 mm and 1.0 mm (kitchen components), deburring of stainless steel pieces, and incision of protective film without marking the stainless steel surface.
The machine consists of an enclosure made of sound-absorbing panels with a safety door. Inside, it houses a 6-axis anthropomorphic robot (165 kg payload capacity) from Motoman (Yaskawa), a plasma welding station, six grinding stations for welds (with pneumatically compensated rollers), two edge grinding stations (with oscillating fork mechanisms), a satin finishing station with axial oscillation (featuring a Scotch-Brite brush Ø 500 mm x 1200 mm), and a free-belt deburring station.
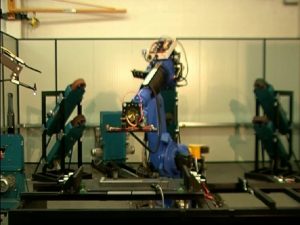
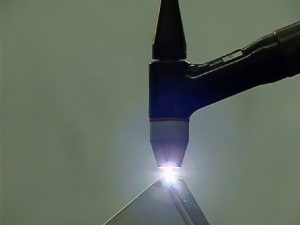
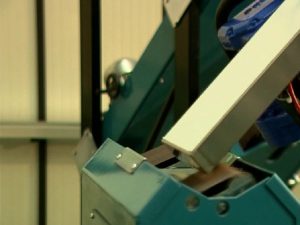
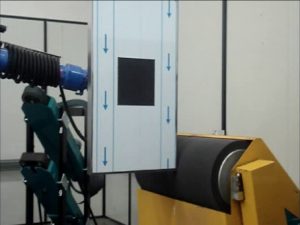
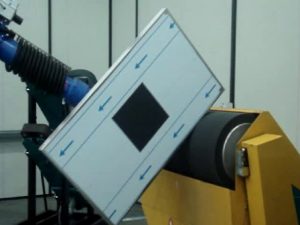
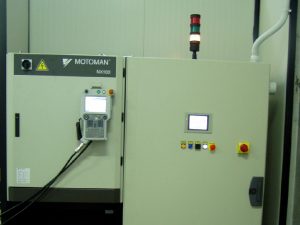
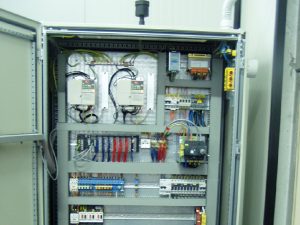
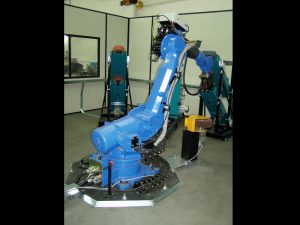
ARNSBERG - GERMANY
2009
Robotic cell for welding and surface finishing of stainless steel parts with thicknesses of 0.8 mm and 1.0 mm (kitchen range hoods).
The machine consists of an enclosure made of sound-absorbing panels, equipped with a safety door, roof, and internal lighting. Inside, it houses a 6-axis anthropomorphic robot with a 165 kg payload capacity, brand Motoman (Yaskawa), two conveyor belts for loading and unloading parts, a plasma welding station, six grinding stations for welds with pneumatically compensated rollers, two edge grinding stations with oscillating fork mechanisms, one satin finishing station with axial oscillation using Scotch-Brite, and one fixed satin finishing station. The system also includes a cartridge dust collector with ten electronically controlled suction ports. Control is managed by a Siemens PLC.
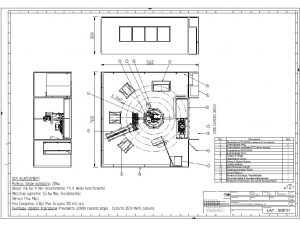
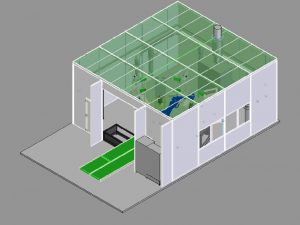
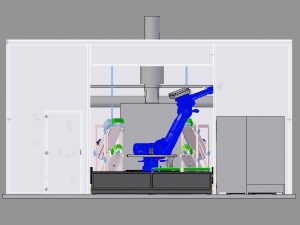
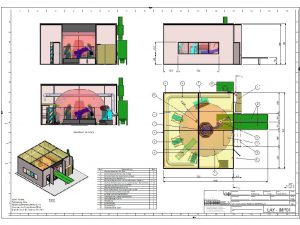
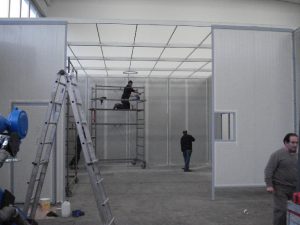
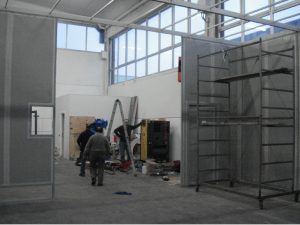
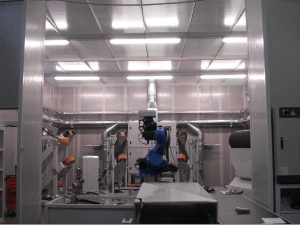
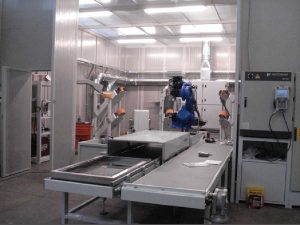
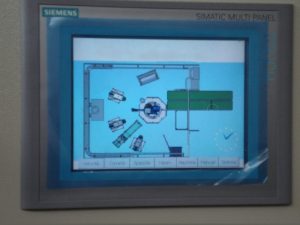
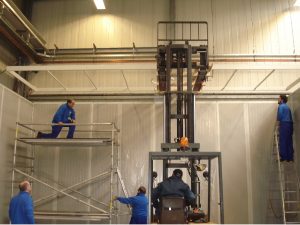
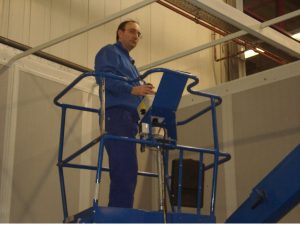
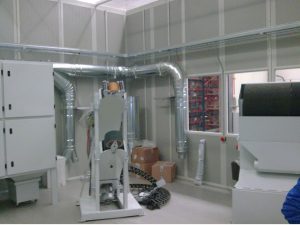
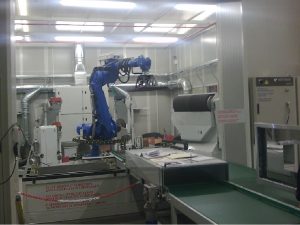
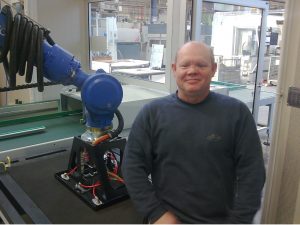
BRESCIA - ITALY
2011
Automatic machine for chamfering clutch discs.
Machine for chamfering clutch discs with diameters ranging from 90 mm to 380 mm and thicknesses from 1.5 mm to 12 mm.
The machine consists of an enclosure made of metal mesh panels with a sliding safety door. Inside, it features a central chamfering unit with two free-belt heads (2.2 kW each), a toothed belt conveyor system coated with polyurethane, and a motorized, electronically controlled format change system. It also includes an adjustable destacker for stacks up to 500 mm in height and 100 kg in weight, as well as a stacking unit with an output conveyor belt that also serves as a discharge buffer.
The enclosure includes two electronically controlled doors located at the entry destacker and the exit stacker. The control system is operated via an OMRON PLC.
BRESCIA - ITALY
2012
Automatic machine for outer diameter grinding and chamfering of clutch discs.
Performs outer diameter grinding and chamfering of clutch discs with diameters ranging from 90 mm to 380 mm and thicknesses from 1.5 mm to 12 mm, and automatically loads them into the machine.
The machine consists of an enclosure made of metal mesh panels with two sliding safety doors. Inside, it contains two main processing units—one for outer diameter grinding and one for chamfering—equipped with four free-belt heads (2.2 kW each). It features two toothed belt conveyor systems with polyurethane coating, two motorized and electronically controlled format change systems, and two adjustable destackers for stacks up to 500 mm in height and 100 kg in weight, which converge onto a single loading conveyor.
An output stacking unit feeds a positioner (tilting loader), which in turn supplies the existing planetary grinding machine. The enclosure also includes two electronically controlled doors aligned with the input destackers. The system is controlled by an OMRON PLC.
EINDHOVEN - THE NETHERLANDS
2012
Edge trimming and deburring machine for steel plates.
Performs surface finishing and edge deburring of steel plates, a necessary process to prevent cracking during subsequent bending operations of the part (fuel tank omega bracket).
The machine consists of an enclosure made of sound-absorbing panels, equipped with three safety doors, a roof, and internal lighting. Inside, it houses an edge grinding machine with four roller heads featuring pneumatic compensation and vertical oscillation, as well as two dual free-belt heads set at +45° and -45° for edge deburring.
It includes a motorized format change system, bearing-guided rails, a motorized roller table for material input, and a motorized roller table for output of the finished material. Additional components include an over-thickness detection roller, cartridge filter system, and ducting for the dust extraction system.
At the output, a 5-axis anthropomorphic Fanuc robot with a 100 kg payload capacity, enclosed in a metal mesh safety cell with photoelectric barriers, performs automatic palletizing of the finished parts.
The control system is managed by a Siemens PLC and Siemens inverters.
TROYES - FRANCE
2013
Weld bead removal machine for conical rods.
Automatic inline weld bead removal, synchronized with the welding process of conical poles made from rolled sheet metal, up to 13 meters in length.
The machine consists of a metal mesh panel enclosure that houses a metal frame supporting a roller conveyor system (with speed synchronized to the output speed of the customer’s welding machine), two abrasive belt heads, and a pneumatic compensation system for head weight. It also includes grinding residue extraction hoods, two pneumatic roller-based pole centering systems, an air filter with spark separator, and extraction ducting.
taichung - taiwan
2013
Robotic cell for grinding and satin finishing.
Perform weld grinding and surface finishing of stainless steel sheet parts (kitchen range hoods).
The machine consists of an enclosure with a safety door (provided by the customer) housing a 6-axis anthropomorphic robot with a 165 kg payload capacity. It includes a loading area and an unloading area, both protected by safety photoelectric barriers.
Inside, there are six weld grinding stations with pneumatically compensated rollers, two edge grinding stations with oscillating fork mechanisms, one satin finishing station with axial oscillation using Scotch-Brite, and one fixed satin finishing station.
The existing customer-supplied vacuum filter system is connected to a ducting system with 10 electronically controlled suction ports. The control system is managed by an OMRON PLC and OMRON inverters.
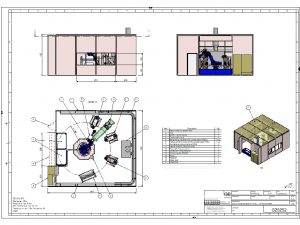
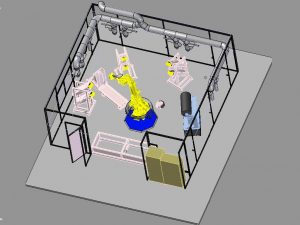
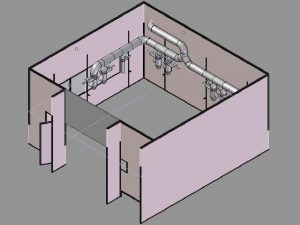
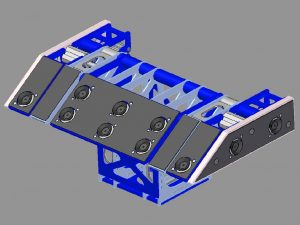
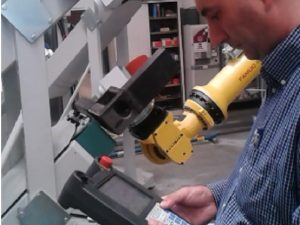
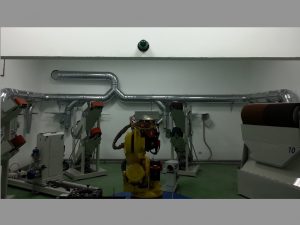
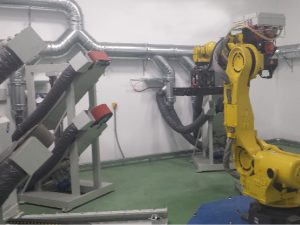

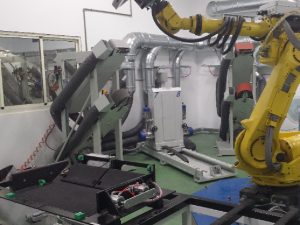
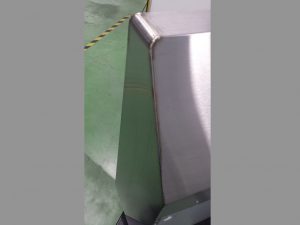
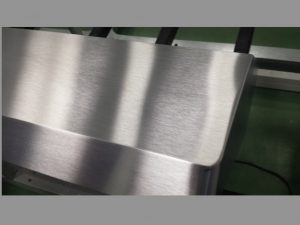
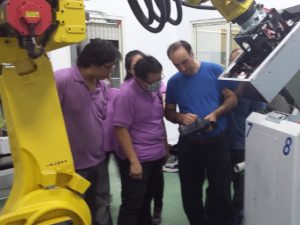
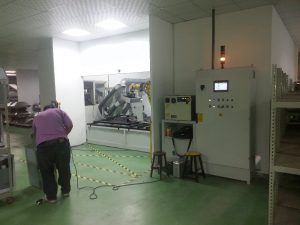
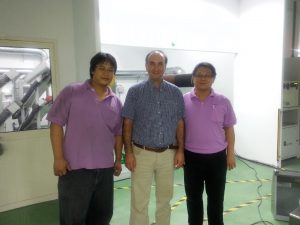
bangkok - thailand
2014
Automatic grinding machine for electrical metal cabinets.
Remove excess weld at the four front corners and grind a radius on one of the side edges of electrical metal cabinets measuring up to 1200 mm x 1200 mm x 300 mm in depth.
The machine consists of a work line with two stations that operate simultaneously, along with an input roller table and an output roller table.
The first station includes a polyurethane-coated toothed belt conveyor, a single-axis automatic format change system, and a grinding head with an oscillating fork and automatic vertical translation.
The second station features a polyurethane-coated toothed belt conveyor, a dual-axis automatic format change system, and four grinding heads equipped with pneumatic shoes and motorized transverse oscillation.
gornja radgona - slovenia
2014
Automatic Grinding Machine for Containers.
Remove excess weld from the floor and roof structures of residential containers up to 40 feet in length.
The machine consists of an infeed roller table with motorized chain transmission, incremental encoder, pneumatic alignment system with rollers, and pressure rollers; a central roller table with motorized chain transmission and incremental encoder; and an outfeed roller table with motorized chain transmission, incremental encoder, pneumatic alignment system with rollers, and pressure rollers.
It includes two transverse grinding heads equipped with 7.5 kW motors, abrasive belts measuring 7500 mm x 200 mm, each with two pneumatically compensated shoe-roller units, motorized via rack and pinion with incremental encoders; and two longitudinal grinding heads with 5.5 kW motors, abrasive belts measuring 3000 mm x 200 mm, each with one pneumatically compensated shoe-roller unit, also motorized via rack and pinion with incremental encoders.
The system features four motorized vertical positioning units for the grinding heads, equipped with ball screw drives, linear guides with recirculating ball bearings, and incremental encoders.
The control system is managed by a Siemens S7-300 PLC and Mitsubishi inverters, and includes safety light curtains and interlocked safety door control.
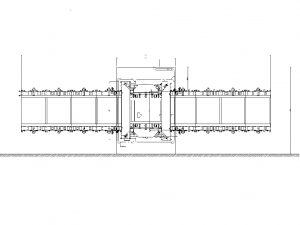
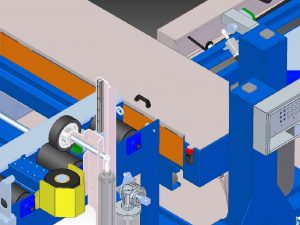
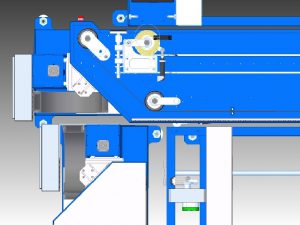
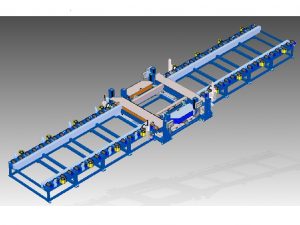
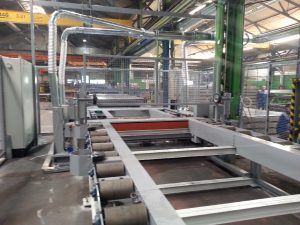
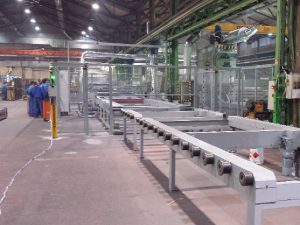
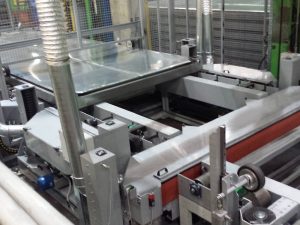
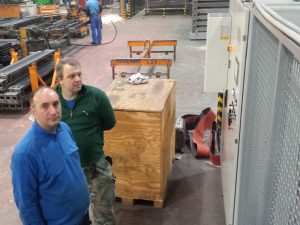
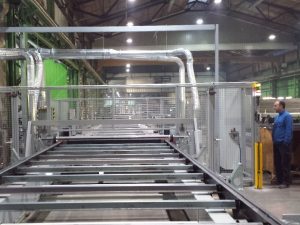
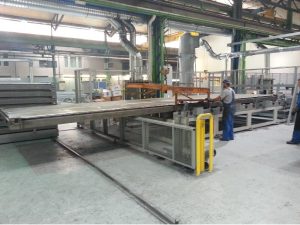
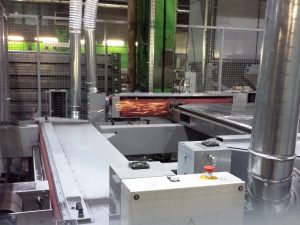
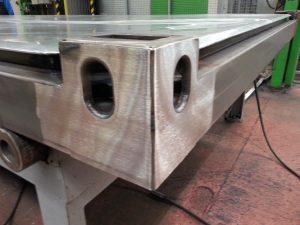
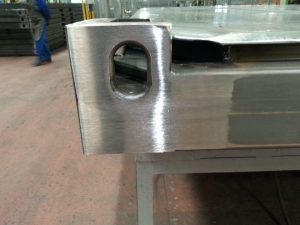
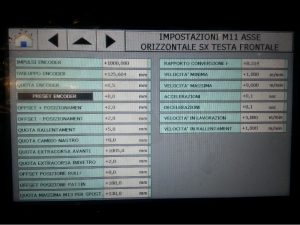
suzhou - china
2015
Automatic Grinding Machine for Scissor Blades.
Perform double-sided grinding of scissor blades of various shapes, thicknesses, and dimensions.
Required productivity: 7,200 pcs/h.
The machine consists of a feeder unit with one set of four removable cartridges for each blade model, a metal frame, conveyor belt, and a pneumatic pressure system for the stacks; and a processing unit (machine) composed of an enclosed metal structure, with infeed and outfeed conveyor belts, four abrasive belt grinding units with transverse oscillation and pneumatic belt tensioning, abrasive belt thickness adjustment, pressure roller group, magnetic conveyor belts, a demagnetizing unit at the outfeed, dust extraction ports, safety micro-switches on access doors, a safety band on the infeed conveyor, and a motorized thickness adjustment system.
Control system operated by a PLC.
jesi - italy
2016
Double-Sided Grinding and Brushing Machine for Copper Bars.
Perform surface finishing on both sides of copper bars with variable lengths ranging from 80 mm to 3000 mm, coming from the punching and cutting machine.
The machine consists of a metal structure with safety enclosures, an infeed conveyor belt, an outfeed conveyor belt, an upper grinding unit and two upper brushing units (with opposite rotation), a lower grinding unit and two lower brushing units (with opposite rotation), pressure rollers, and dust extraction ports. At the outfeed, there is a pneumatic transverse pusher unit.
numana - italy
2017
Robotic Grinding and Brushing Cell for Workpieces with Automatic Positioner.
Perform weld grinding and surface finishing of stainless steel parts. Perform surface finishing of large parts with an automatic positioner.
The machine consists of a sound-absorbing panel enclosure with a safety door, ceiling, and internal lighting. Inside, it contains a 6-axis anthropomorphic robot with a 165 kg capacity, an automatic positioner with 3 positions, 4 grinding stations for welding with pneumatic compensation roller, two free belt grinding stations, one satin finishing station with Scotch Brite and axial oscillation, and one fixed satin finishing station. It also features two mobile grinding heads (on the robot’s hand) with a pneumatic compensed pad, as well as a storage station for gripping organs with a quick-change system. A cartridge vacuum, duct system with 8 electronically controlled suction outlets, and a control system with an OMRON PLC are also included.
AZZANO DECIMO - italy
2017
Metal Strip Deburring Machine.
To perform deburring of steel strips with widths ranging from 20mm to 150mm.
La máquina está compuesta con una base de acero soldado, un sistema de cambio formato automático (ancho de la banda), dos cabezales dobles de cinta abrasiva libre (+45º y -45º) y dos cabezales de rodillo para esmerilar el canto. Un sistema de transporte motorizado de la banda metálica y un sistema de control con PLC.
rho - italy
2018
Automatic Feeding and Positioning Machine for Press.
To automatically feed aluminum plates into a press and position them step by step. Required precision: 0.05 mm.
The machine consists of a motorized destacking unit (for stacks up to 500 mm) with suction cups, a roller feeding unit with pneumatic clamping gripper, a positioning system with servo motor and ball screw drive, and a control system with PLC and touchscreen command panel.
bergamo - italy
2021-2022
Aluminum Sheet Die-Cutting Machine
It performs the die-cutting of aluminum sheets coated with printed paper, aligning the cut based on the printed pattern.
The machine consists of an enclosure with metal mesh panels and safety doors, an automatic de-stacker with vacuum suction cups, a 3-axis optical alignment unit, a 2-axis Cartesian manipulator, a hydraulic die-cutting press, an output conveyor, and a PLC-controlled control panel.